長尺物の外径切削・外径研磨・外径研削でお困りでは?
低コスト・高能率で可能だとしたら?
未知の世界があるとしたら?
はじめに
はじめに研削ベルトの性質、及び、研削ベルトでどのような仕事ができるかを紹介させていただきます。研磨布紙、または研削ベルトに関する認識は、金属加工に関係されている方々の間では、
まだまだ一般的には「サンドペーパーに毛の生えたようなもの」という認識の方が多いのではないでしょうか?
しかし、最近日本でも研削ベルトに対する認識が高まってきた様に感じられます。研究熱心な方ならば各地で開催される機械展をご覧になって、研削ベルトを使用した機械の前で足を止められたことが2度や3度おありになると思います。
先に「日本でも」と申し上げましたのは、欧米では研削ベルトを使用した工作機械を工程に組み入れて考えることが既に常識化しているからです。
既にアメリカでは1964年から、西ドイツでは1962年から、それぞれ研削ベルトの生産額が研磨砥石の生産額を上回る様になりました。
また、American Machinist Inventory of Metal working Equipmentの数字に基づく統計によると、アメリカでは砥石を使用したグラインダーの伸び率は208%を示しております。
日本の工作機械は数値制御の応用など世界最高水準を行く分野もありますが、こと研削ベルトに関しては発展途上の国といえるのではないでしょうか。
この発展途上の状態を解決する為にも、
1.現在の研削ベルトがいかに優れた性質を持っているか
2.研削ベルトを使用した機械でどのような仕事ができるのかについて、皆様の認識を新たにしていただくことが、何より必要なことかと思われます。
それ故、以下にセンターレスベルト研削盤(センタレスベルト研削盤)について大要を紹介させていただきます。
研削ベルトについて
研削ベルトの起源についてはCoated Abrasive Modern Tool
Industryに紹介されているところによると中国では13世紀頃すでに
天然ゴムを羊皮紙に塗り、それに貝殻の粉末をつけたものを使用した
記録があるとのことですが、そのような古いことはさておき、近代に
なってからではおおよそ19世紀前半には、イギリス・フランス・
アメリカなどで、或いはエメリーペーパー又はサンドペーパーの
名称によって実用に供せられるようになり、一部では機械に装置され
始めて家具パネルの塗装前の工程、合板の広範な表面積の表面研磨に使用される程度でした。
それが第二次世界大戦を契機として金属加工に使用されるようになり、俄然その生産が伸び始めました。これは化学分野の進歩により砥粒、基材及び接着剤(下図を参照)が改良され、
また砥粒の電気植付等の技術開発がなされたことによって、工作機械用工具としての優秀性が飛躍的に進歩したことによるものです。
では、現在の研削ベルトがどのように優れた性質を持っているかについて若干述べてみましょう。
帯状の研磨布紙の両端で接合しベルト状にした研磨工具のこと
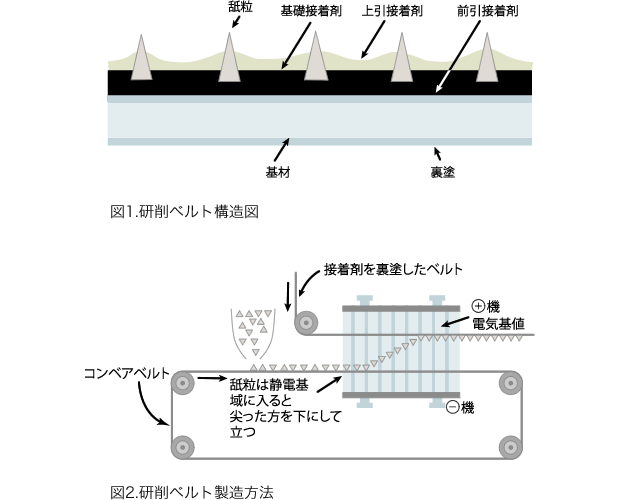
Ⅰ.研削量が大きい
後ほど使用例のところで紹介いたしますが、φ100長さ6mの鋼管の黒皮はぎに使用できるほどです。では、なぜ研削ベルトに何故そのように大きな研削力があるのかということに付いてはもちろん理由があるわけですが、
- ①その第一の理由は研削ベルトでは個々の砥粒は必ず尖った鋭利な方が外に出るように付着しているからです。
- 面図は絵だから格好よく見せているのではありません。声はH接着剤を塗ったベルトに砥粒をつける場合静電気を利用して砥粒に一定の方向を与えているからです。図2をご参照ください。)
- ②ベルトの弾性によって
- 1)加工物に対し個々の砥粒刃が有効に働き
2)更には目詰まりを起こしにくいからであります。
特に②の2)に付いては銅のような軟い粘り気のあるものを砥石で研磨した場合と比較してみれば分かることです。
Ⅱ.仕事の質がよいこと
- ①ベルトの周長を長くしたり、また油、水などによる湿式加工ができることによって、冷却性が維持できるため加工物の表面組織の変化や歪が少ない。
- ②ベルトを取り替えることによって加工物の仕上げ面の選択ができる。砥粒の小さいものを使用すればバフ工程の仕事もできる。
(例えば600番の研削ベルトを使用すればSK材で表面粗さ0.4μ程度のものが得られる)ということになります。
Ⅲ.取り扱いが便利
これは砥石の場合と比較してみれば容易にご理解願えることと思います。
- ①砥石のようにドレッシングをしたり、バランス取りをしたりという煩わしさがありません。
- ②砥石は割れて飛散した場合、その危険性はご承知の通りですが、研削ベルトはその点きわめて安全で初心者に操作をさせても安心です。
以上、研削ベルトの長所を述べてまいりましたが、世の中には長所のみ、またはその反対の短所のみというものは存在しないようです。研削ベルトにも泣き所があります。
それは砥石ほど精密度が出ないということです。たとえば加工物に千分台の精密度を要求される場合には研削ベルトではちょっとお手上げのようです。
しかしこの欠点はコンタクトホイールの硬さを選ぶことによって相当程度まで(2/100程度まで)カバーすることが出来ます。
この辺りでそろそろ手前味噌に入らせていただきましょう。
中部機械株式会社では、前に述べた研削ベルトの長所を生かし短所を補った丸材加工の機械、すなわち「センターレスベルト研削盤」を昭和39年より研究開発してまいりました。
実際にこれがどのうな使い方をされているかについて、皆様方のご参考になればと思います。
弊社CG型センタレスベルト研削盤の使用例
本機の活躍する分野は広範囲に及びますが、その使用例をあげながら説明します。
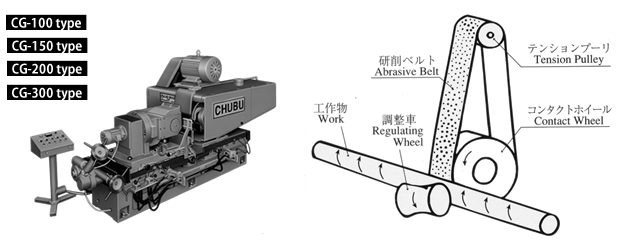
Ⅰ.鋼材及びステンレス材について
- ①旋盤作業に換る仕事
- 丸材の外形寸法を出す場合、一般には旋盤加工により一皮剥ぐ方法が行われていますが.これを素材寸法を再検討(削り代を小さく)し、本機に置き換えることによって生産性を向上させることが出来ます。
- 例1)某ベアリングメーカーにて:
- 周知のようにベアリング鋼は材料表面に脱炭層があります。コロベアリングのコロを製造している工場では、この脱炭層を除去し焼入れ性を良くするために、まず自動盤で外径旋削し突っ切り加工してコロの素材を作っていました。 これを長尺材のまま本機により外径研削のみ行い、単能盤で突っ切り加工してコロを得るように工程を変えました。 その結果、外径旋削では送り速度0.3m/min(回転数1500r.p.m.×送り0.2mm/rev)であったのが、本機では送りを2.5m/minで行えるので生産性は8倍強となり、従来下請工場にも出していた仕事が自社内で楽にできるようになりました。
- 例2)某織機メーカーにて:
- 小物バー材の外形寸法を決めるのに、旋盤により寸法きめの上ヘール仕上げしていたのを本機に置き換えて 例1)とほぼ同等の効果を収めることが出来ました。
- ②砥石研削盤に換る仕事
- 例1)某自動車用バネメーカーにて:
- 品質の向上を図るため、引き抜き黒皮のバネ鋼素材を砥石センターレス研削盤で加工していましたが、研削能力不足及び砥石割れの危険のため送り速度を速めることが出来なかったので、 本機に置き換えましたところ、2.5倍に生産性を高めることが出来ました。
- 例2)某ステンレスパイプメーカーにて:
- 繊維、染色、製紙用等のパイプロールを厚板より成形溶接し、矯正機にかけた後、砥石センターレス研削盤にて仕上げ面まで加工していましたが、周知のようにステンレス材は非常に研削しにくく、 仕上げ面もきれいに出来なかったので本機に置き換えました。その結果、加工時間が短縮され仕上げ面粗さ、ツヤもよくなりました。
- 例3)某製鉄所にて:
- 細物ステンレスパイプの外径を研磨して出荷するため、砥石センターレス研削盤で加工していました。しかし送り速度を早く出来なかったので本機を採用いただき、生産性を2~3倍に向上させました。
- 例4)某自動車部品メーカーにて:
- 段付き部品の頭部を焼入れ後、円筒研削盤で両センタ保持して加工し、仕上げ面粗さ3Sに仕上げていました。これを本機に特殊ワークブレード、自動材料供給装置を取り付けたものに置き換えました。 その結果生産性を約5倍に高め、人手も除く事が出来ました。
- ③旋盤+砥石研削盤の複合作業に換る仕事
- 丸素材を旋盤により研削代を残して荒加工した後、砥石研削盤で仕上げるという作業方法を採用されているところが多いと思いますが、これを本機に置き換えれば一台で両方の作業が出来ます。 これにより、旋盤作業におけるチャッキング・芯出し時間の省略、切削能力向上による時間短縮、さらに砥石研削盤よりも本機のほうが切削能力が優れるので、その加工時間もまた短縮できる等、総合して大きな利点があります。
- 例1)某シリンダーメーカーにて:
- 外径φ100×L6,000厚肉パイプを従来は長尺旋盤により長時間かけて素材の黒皮を削り、次に砥石センターレス研削盤にかけて仕上げていました。 これを本機に置き換えたところ、生産性は約6倍に向上し、しかもこの場合取り代を10mmから約2mmに減らすことが出来ました。
- 例2)某フォークリフトメーカーにて:
- フォークリフトについている油圧ピストンロッドを、従来は旋盤加工後、高周波焼入れをし円筒研削盤で仕上げていました。 これを材料購入時取り代が1mm程度になるように押さえて本機に置き換えしたところ、生産性は3倍に向上し、材料は一本当たり約3kgs節約できました。
- ④バフ作業に換わる仕事
- メッキ前のパイプ、ステンレスパイプ等はバフ作業に頼っているのが現状ですが、バフ作業のように汚れる仕事は敬遠されがちで、また生産性も上がりません。 それに対して本機は静浄性、生産性ともに優れており、今後この分野における本機の活躍が期待されます。
- 例1)某エアーポンプメーカーにて:
- エアポンプ外筒メッキの前加工にバフ機を使用していましたが、生産量の増加に追いつけず本機に置き換えました。 この結果、生産量を3倍に増強することが出来ました。この場合、素材が電縫管であり、一気に細い粒度の研削ベルトで仕上げることができませんので、機械を3頭型にしました。 この3頭型とは標準機を3台並列にするところを、同一ベッド上に研削部3台分を取り付けて1台の機械としてまとめ上げたものです。 この場合、材料供給側ヘッドより順次研削ベルトの砥粒番手を細かくすることにより、ワンパスで荒・中・仕上げ加工が出来ます。
- 例2)某繊維機械メーカーにて:
- 薄肉パイプの外周面を糸が走る部品があります。この表面は小さな傷がついていても糸が切れるので、慎重にバフ加工されていました。 これを本機の採用に踏み切ったことにより、未熟練工でも表面粗さ0.4Sのものが簡単に得られるようになり生産性は10倍以上に向上しました。
Ⅱ.特殊材料関係
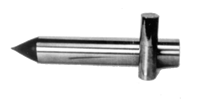
①シリコン単結晶
半導体用シリコンの結晶生成時、円筒面が不揃いで硬い酸化膜が出てきます。これを除去成形するのにする作業に本機が威力を発揮しています。これは他の加工方法では加工熱のため内部歪、クラック等を生じて製品の特性にばらつきが出るからです。
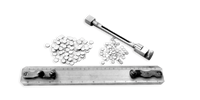
②電気抵抗体
直径4~20mm極薄円筒板の外周部を研削するために、特殊ワークブレードを本機に取り付けて加工するように工夫してみました。以前は機械化できなくて人手により外周部を磨いていたので、その生産性の向上は比較になりません。
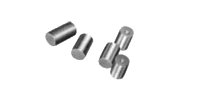
③磁石鋼
磁石鋼の外径を研削するのに砥石センターレス研削盤で加工していました。ところがこの素材は硬くてもろい為、一回あたりの取り代を増すと素材が割れたり端面がかけたりするので、少しづつ切込み7~8パスして仕上げていました。そこで本機に切り替えたところ、2パスで仕上げるようになりました。というのは研削ベルトは弾性切削を行うため、重切削をしても素材が割れたり欠けたりする心配が少ないからです。
④セラミックパイプ
特殊セラミックパイプの外径を本機で加工しています。これは前記③の磁石鋼と同様、割れやすいので他の方法では加工が難しいからです。
⑤ジルコニュームパイプ
このパイプは原子燃料用カプセル等に使用されるもので、非常に酸化しやすく砥石などでは加工熱が出て歪を生じるため加工が大変難しいのです。しかし研削ベルトならば砥石に比べて研削性も優れ、発熱もはるかに少ないため、この外形加工が大変容易に行えるようになりました。
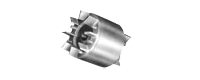
⑥アルミニューム
砥石では目詰まりを起こして加工できませんが、研削ベルトでは殆ど目詰まりしないので好都合です。例えばダイキャストされたモーターローターの外径の一皮剥ぎに本機を使用しています。
⑦銅合金
前記⑥のアルミニュームと同様、砥石では研削できないので、研削ベルトが活躍する材料です。例えば伸銅丸棒の表面を従来は化学的に酸洗い処理をしていましたが廃液処理の問題もあり、本機に置き換えさっぱりしたということです。
⑧グラスファイバー
研削ベルトの研削性の良いことを生かして工作作業を可能にします。加工例としては地下埋設ケーブルの保護パイプや釣竿などがあります。なお、釣竿はテーパーになっているので、テーパー研削ができるように一部改造しました。
⑨カーボン棒
乾電池用電極のカーボン丸棒は射出成形のため表面がやわらかすぎます。この表面を一定仕上げ面に粗さにするため、本機で一皮剥ぎ取ることにしました。また、発電機用ブラシを従来は旋盤加工していたのを、本機に置き換え外形加工を行っています。
むすび
以上、弊社センタレスベルト研削盤の使用例の数々を紹介してまいりましたが、いかがでしょうか。労務費諸経費は年々増す一方で、我々は厳しい経済環境下に置かれています。工場の合理化・生産性の向上に日夜取り組んでおられる皆様方におかれましては、新たな目をもって今一度ご自分の工場内部を再検討された上、センタレスベルト研削盤を導入する余地がないかじっくりとご思案願います。弊社ではテスト加工サービスを行っております。弊社のテスト機にてテスト加工を行った後、データをお付けしてご返送いたします。是非、ご利用ください。